“If we don’t make it before the harvest, we’ll have to postpone the entire ERP project.” That was the clear message Columbus received during a meeting with Smaken av Grimstad. Just eight weeks later, the entire ERP cloud migration was completed – on time and within budget.
When the board decided to lift the ERP solution to the cloud, there were only two months left until the harvest in July. “Cucumber production starts on July 25, marking the beginning of the harvesting season. We had to be production-ready, otherwise we would have had to delay the project,” says Jan Rommetveit, CEO and co-owner at Smaken av Grimstad.
Columbus and Smaken av Grimstad have maintained a strong customer relationship for over 10 years. “Fast is one of Smaken av Grimstad’s values, and we really got to experience that. We’ve never delivered an ERP cloud lift in eight weeks before,” says Per Christian Øen, Customer Manager at Columbus.
Sustainable from farm to table
The story of Smaken av Grimstad started in 1917, founded by local farmers and businessmen with the purpose of "canned fruit and vegetables". In 2012, Grimstad Konserves AS changed its name to Smaken av Grimstad AS. By 2022, the company had a turnover of 115 million NOK and was supplying products to large households, the industrial sector, and the grocery market.
“We’ve been sustainable long before the term was first introduced in 1987 by the Brundtland Commission”, says Rommetveit. “Throughout history, we’ve collaborated with local growers in the Grimstad area. When the raw materials are harvested, they’re driven a few kilometres by tractor before being delivered to the factory.”
Overripe for change
“We have investment and implementation plans, and the old ERP system has been on our ‘should-do’ list for a long time,” says Rachel Mentzoni, CFO at Smaken av Grimstad.
The last upgrade of the ERP system was in 2018, and it’s used across the entire business, from purchasing raw materials and warehouse and production planning to sales, invoicing and accounting. There were several factors that suggested it was time for a change and Smaken av Grimstad had stretched the "ERP system rubber band" as far as it could. The company decided to opt for Infor CloudSuites industry solution for the food industry.
- Food & Beverage
- Norway
- Case
- Finance & Supply chain
Summary
Smaken av Grimstad faced daily challenges navigating its outdated on-premises solution. Critical integrations were intricately linked to its operations, making upgrades a complex task. Smaken av Grimstad was presented with a choice between an eight-week project timeline and a six-month timeline, with the go-live date positioned either before or after the company’s peak season. Opting for a go-live before the peak season, the full upgrade from Infor M3 13.4 to Infor M3 CloudSuite was completed in eight weeks. Despite the tight schedule, Smaken av Grimstad successfully reached the go-live milestone while streamlining operations and providing an efficiency boost.
About Smaken av Grimstad
Smaken av Grimstad specialises in the production of canned vegetables, berries, potatoes, red cabbage, and pizza sauce. Established in 1912, Smaken av Grimstad focuses on creating quality food items with an extended shelf life from fresh and nutritious raw materials. By 2022, the company had a turnover of 115 million NOK and was supplying products to large households, the industrial sector, and the grocery market.
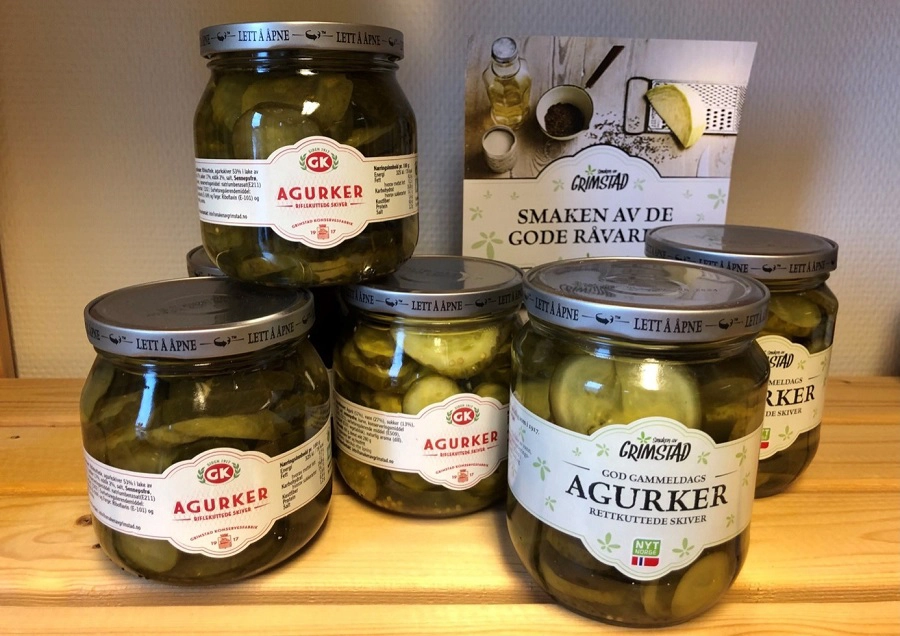
“The bank informed us that remittance files had to be updated to a new format, with a deadline of April 1, 2024, and changes in VAT reporting requirements had increased our manual workload,” explains Mentzoni. “We also had challenges with tracking input factors from farm to table, which is critical for us to have control over as a responsible food producer. The outdated ERP solution was holding us back. We couldn’t wait any longer.
Accelerated cloud lift
Making the production start was the most critical aspect. Cucumbers are ripe and ready for harvest around mid-July. A few days later they start to rot. This means the factory must be set up with people and systems, ready to receive the raw materials when they’re harvested. To ensure business liquidity, the order and invoicing system had to be in place.
“Moving the ERP system is like a complicated heart operation, but with skilled people we were never worried,” says Rommetveit. “Columbus knows us well and had done excellent preparatory work. The collaboration worked perfectly.”
Despite thorough preparatory work, the project experienced a critical element that had to be handled, otherwise the cloud lift would be postponed. “It was about the warehouse’s ability to scan pallets in connection with the delivery of the goods and to receive electronic information about goods deliveries for the customers. Without this in place, our customers would have to do this manually - an exercise that our large food wholesale customers Norgesgruppen, Rema and Coop wouldn’t accept,” says Rommetveit.
The harvesting of cucumbers starts on July 25, which is also the starting signal for the production season at Smaken av Grimstad.
With a tight timeline, the risk increases, and Columbus highlights two critical factors that contributed to the project being completed on time and within cost. “One is the team effort behind the cloud lift or the ‘we-effort’", says Vidar Furuborg, Project Manager at Columbus. “It wasn’t ’us and them’, but ’we’ all the way. Many were involved in the project. Accurate resource allocation and secure, timely data migration were key factors. Having the right expertise in place also made a big difference. Professional project management, combined with an agile approach and close team collaboration, brought everything together for a successful outcome.”
“The other factor was that we decided early on to do a 1:1 lift, i.e, to lift today's solution ’directly’ up to the cloud. This was the best approach and the most appropriate for Smaken av Grimstad, and we base the cloud lift on proven project methodology for Infor's solutions. When we get to the cloud, Smaken av Grimstad knows what awaits them there, and when we are in operation, we can work on developing new functionality,” explains Furuborg.
The solution's farm-to-table perspective
Infor Cloudsuite Food & Beverage, operated in the cloud by Amazon Web Services (AWS), offers a highly competitive advantage with its low operating costs. Additionally, Infor continuously updates the solution with industry-specific content tailored to meet the needs and requirements of food and beverage manufacturers worldwide.
“Infor's multi-tenant cloud solution has a value proposition that resonates well with customers. They benefit from a solution with built-in functionality, security, compatibility and stability ’included’. This also explains why they are gaining ground in the ERP market worldwide,” says Per Christian Øen, Customer Manager at Columbus.
“The solution takes care of our historical farm-to-table perspective by allowing us to obtain insight from the entire supply chain,” says Rommetveit. “It’s also equally important that we’re in operation with access to functions that are relevant today. We know that the solution is constantly enriched with industry-specific functionality that makes us confident that we have a future-proof platform that will always be relevant to our business. It hasn’t cost us more than a decent tractor, proving that modern ERP platforms are now accessible for SMBs like us.”
Governance in a new context
The new ERP solution is updated regularly with new functionality. This means Smaken av Grimstad will, in practice, have new opportunities to perform actions differently across the entire organisation or internally in purchasing, production, warehouse and finance functions.
“If we’re to keep up the pressure, we must be ’on’ all the time,” says Rommetveit. “There’s always room to improve business processes, but it must be managed in a new way than before, and this is about governance in a new context.”
“I completely agree with what Rommetveit raises. It’s a topic that many become aware of when they move to the cloud,” says Øen. “The key is to develop a governance model that anchors, communicates and implements new functions in the ERP system in line with their own business development. This also affects our role, where we often contribute with ongoing advice on which functions should be ’turned on’, while using our implementation methodology that ensures that we involve and include the organisation.”
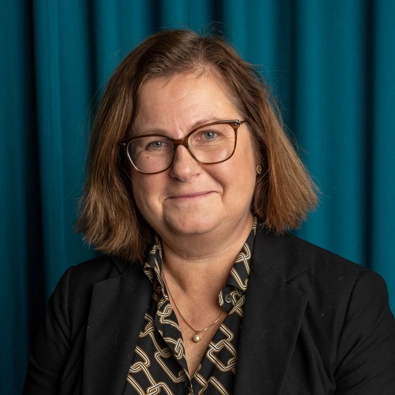