With increasing regulations, higher quality standards, and the critical responsibility of keeping patients safe, the MedTech industry is under more pressure than ever. On top of this, the extensive documentation required for each process creates a constant challenge to maintain control over operations without sacrificing efficiency.
However, the rise of new technologies offers MedTech companies an opportunity to transform the way they work. From improving processes to navigating regulations more effectively, these tools are helping businesses not only meet standards but exceed them.
In this blog, we spoke with Mikael von Porat, Senior Business Consultant at Columbus, and Kevin Bull, Product Strategy Director at Columbus, to discuss actionable ways MedTech companies can optimize their operations, stay ahead of regulations, and adopt best practices to drive success.
Streamline manufacturing with validated and controlled processes
In MedTech, every action you take must be recorded and documented. Yet, according to Mikael and Kevin, many companies still rely on manual processes, which can create challenges in maintaining traceability and compliance.
“From my experience with customers, the main issue is that a lot of documentation is still on paper,” Mikael explains. “The big challenge is moving to electronic records or electronic batch records for the whole manufacturing process, where all evidence of compliance is collected digitally.”
This shift to digital records also supports validated manufacturing processes, a big part of MedTech quality assurance (QA). QA makes sure that every process, record, and update aligns with compliance requirements throughout a product's lifecycle.
“There’s a saying in the industry: If it’s not documented, it didn’t happen,” says Kevin. “It’s no good saying, ‘Yes, we checked this’. It has to be documented and auditable. That’s a key difference with MedTech - there’s a level of checking and validation that’s almost ‘on steroids’.”
There are also several regulations, like EU Annex 11 and CFR 21, which you, as a MedTech company, already know play a critical role in maintaining compliance and keeping patients safe.
But beyond knowing these regulations, how you operationalize them is what truly matters. That’s where records like electronic batch records (EBRs) come in. These manufacturing records are essential to your compliance strategy, providing the traceability and accountability regulators demand.
Managing these records manually can be a significant challenge, given the volume of documentation involved. “Validating core business systems to handle this is complex, which is why many companies stick with paper,” says Mikael. “It seems easier for many, even if it’s less efficient.”
By moving to digital solutions, you can not only simplify how you manage these records but also reduce the risk of errors and improve traceability – all key factors in maintaining compliance and driving operational efficiency. “Modern technologies support electronic signatures and approval processes. This means you can rely less on manual documents by using the system’s digital components, streamlining the quality release process,” adds Mikael.
Kevin points out that paper-based records might feel like a safe fallback for MedTech, but they come with serious risks. “Paper records can get lost, damaged, or go missing. They’re not sustainable, either, and companies must keep records for at least ten years. One manufacturing order alone can result in a binder several centimeters thick.”
The move to digital records not only reduces these risks but also improves efficiency. “We’re not eliminating steps,” says Kevin. “We’re verifying every step electronically. That’s why I would recommend getting as much as you can into a digital system and move away from paper.”
Connect supply chains for full tracking and traceability. Current global geopolitical tensions have significantly impacted the MedTech industry, resulting in many companies resizing their supply chains and rethinking their global manufacturing networks.
“MedTech companies are increasingly focused on building supply chain resilience,” says Kevin. “This means adopting technologies that can adapt to unexpected shocks – whether they’re political, environmental, or logistical. This is prompting more companies to consider nearshoring for greater control.”
Mikael also points out that managing the tracking of components, batches, and materials across the entire lifecycle is becoming increasingly complex, particularly when supply chains are more interconnected than ever. Adding to this challenge is the need to collect accurate data from multiple sources and achieve complete transparency for every stage of a product’s lifecycle.
“In the past, achieving full visibility wasn’t always straightforward,” Mikael explains. “But with modern traceability tools, you can now gain a much clearer view of your entire supply chain. These tools not only track a batch number and map its journey within minutes but also consolidate data from several sources into one unified view. That level of insight can save time, reduce risk during an audit, recall, or quality issue.”
Digital product passports (DPPs) are also becoming increasingly important in meeting regulations where traceability is key. By centralizing information such as expiration dates, material reusability, and compliance data into one accessible record, DPPs make it easier to track and share critical information across the supply chain. Mikael and Kevin also highlight that certain materials have expiration dates which need to be tracked and managed.
“Core business technology such as ERP can also support tracking these materials,” says Mikael. “For example, if you’re dealing with expired plastics, modern tools can help you decide whether to revalidate or scrap them. This isn’t just about compliance; it’s about minimizing waste and making smarter decisions.”
Kevin adds: “Revalidating expired materials, like sterilizing them for reuse, can introduce additional steps into your workflow. Without a system to manage this, it can quickly become chaotic, especially if expired materials are used incorrectly. Modern technologies help you stay in control and make informed decisions about whether to reuse or dispose of these materials.”
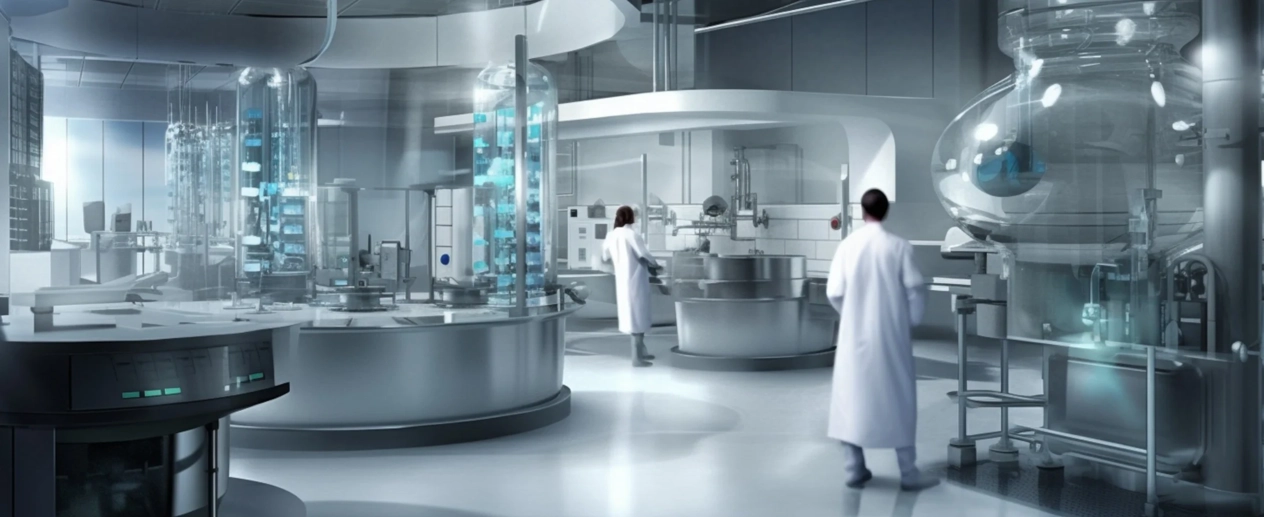
Improve supplier management
With several suppliers to coordinate, and varying levels of criticality for the materials they provide, there’s a need to not only have the right level of oversight but also ability to manage it efficiently.
Mikael highlights that with modern core business technology such as ERP, you can integrate supplier approvals, audits, and subcontractor workflows into a centralized system, creating a more agile and transparent approach to supplier management.
“Classification helps purchasing and quality departments focus on what matters most,” Mikael explains. “It’s about tailoring the level of oversight to match the supplier’s role. For example, a commodity supplier might only need basic monitoring, while a critical supplier providing high-risk components may require detailed audits and ongoing reviews. Technology simplifies this by streamlining approvals and automating audit schedules, making sure no supplier falls through the cracks.”
Mikael also points out that recurring audits are essential for maintaining quality over time. “Re-auditing isn’t just a checkbox exercise,” he says. “It’s about consistently verifying that your suppliers are maintaining the standards they committed to, and technology can make this process more efficient.”
Kevin adds: “You need to make sure your subcontractors maintain inventory control and document the movement of components with the same rigor you would internally. Technology can make this easier by integrating subcontractor data into your traceability workflows, creating a clear line of sight throughout the supply chain.”
Optimize equipment management and maintenance
Just as traceability is critical for materials, proactively monitoring MedTech equipment is essential to maintaining product quality and preventing costly downtime. But managing and maintaining machinery across multiple sites can be a challenge.
Kevin points out that modern asset performance management systems make it easier to stay on top of equipment status. “With modern tools, MedTech businesses can oversee machinery status across different factories,” says Kevin. “This provides a real-time view of which equipment is calibrated and validated, so you can maintain compliance and avoid unnecessary risks.”
AI can also help make your equipment management smarter. Kevin highlights how image recognition can validate machine setups, detecting improper configurations that might lead to errors. “With predictive maintenance, AI monitors sensors so you can anticipate failures before they happen and schedule maintenance proactively. This reduces downtime and keeps operations running as they should be. ”In addition to AI, mixed reality (MR) technologies like augmented and virtual reality are transforming how equipment is managed and maintained. MR can provide real-time guidance for machine setups, training, and maintenance processes, helping teams avoid errors and minimize downtime.
While AI has the potential to improve much more than just asset maintenance, it’s important not to adopt AI for the sake of it, says Santosh Kataram, Associate Principal Architect, Data and AI at Columbus. Instead, MedTech companies should focus on identifying use cases with the quickest ROI and prioritize those first. You can read more into defining valuable AI use cases by clicking here.
There are also regulations like the EU AI Act, which marks a major step toward standardized AI governance. With MedTech systems playing a critical role in areas like diagnostics and treatment, they’re classified as high-risk under the Act.
Key requirements under the EU AI Act include:
- Risk management systems to identify and mitigate AI-related risks
- Strict data governance to ensure accuracy, security, and transparency
- Ongoing monitoring of AI systems post-market to maintain compliance
“While the EU AI Act introduces stricter requirements, it’s also a chance for MedTech businesses to show they’re ahead of the curve and are committed to safety, reliability, and delivering trusted solutions in critical areas like diagnostics and treatment,” says Kevin.
Modern technologies also present opportunities for servitization – offering machinery as a service to your customers. This model allows you to provide value-added services like maintenance and monitoring, creating new revenue streams.
Kevin explains how this works: “If a company provides a machine to a hospital but retains ownership, they still need to track and maintain it as if it were in-house. Monitoring failures and scheduling maintenance makes sure the asset performs reliably, which allows the company to charge for the ongoing service.”
Mikael builds on this with a real-world example: “HP, known for computers, also manufactures laboratory analysis machines. They used to sell the machines outright, leaving maintenance to the buyer. Now, they’ve shifted to offering maintenance and validation services as part of the package. In some cases, they even lease the machines and take care of replacements after a few years. It’s a model that adds significant value and strengthens customer loyalty.”
Enabling all areas of MedTech transformation
While we’ve highlighted some of the key areas where new technologies can drive improvements and meet regulatory requirements, large-scale digital transformation in MedTech goes even further. At Columbus, we enable transformation across every part of your business.
Together, we can help you:
- Maintain high-quality management standards – adopt robust quality management practices that align with regulatory requirements and drive continuous improvement.
- Enhance cybersecurity – identify gaps in security and update defenses to protect patient data and maintain regulatory compliance
- Gain financial insights and streamline workforce management – achieve real-time visibility into costs, budgets, and cash flow while equipping your workforce with the training, certifications, and tools needed to maintain production quality.
- Enhance logistics processes – optimize transportation, warehousing, and claims management for smoother operations.
- Create exceptional customer experiences – deliver seamless customer journeys that build loyalty and keep customers coming back.
With the transformation projects we run with our customers, our priority is creating a clear, actionable plan that integrates people, processes, and technology. We understand that every organization’s strategy is unique. That’s why we offer a wide range of advisory services – whether it’s developing a comprehensive data and analytics roadmap or tackling specific business challenges with targeted solutions, we’re here to help.
Fill out the form below for more information on how we can help your business.